1. Einleitung: Die Herausforderung für Standard-PV-Systeme in aggressiven landwirtschaftlichen und Abwasserbehandlungsumgebungen
Die zunehmende Verbreitung von Photovoltaikanlagen zur nachhaltigen Energiegewinnung führt zu einer immer breiteren Anwendung dieser Technologie in unterschiedlichsten Einsatzbereichen. Dabei rückt auch die Nutzung in bisher weniger betrachteten, jedoch potenziell besonders anspruchsvollen Umgebungen wie landwirtschaftlichen Betrieben und Kläranlagen in den Fokus. Diese Bereiche verfügen häufig über große, ungenutzte Dach- oder Freiflächen und weisen einen beträchtlichen Eigenbedarf an elektrischer Energie auf, weshalb die Installation von PV-Anlagen dort aus wirtschaftlicher und ökologischer Sicht sinnvoll erscheint.
Allerdings unterscheiden sich die Umweltbedingungen an solchen Standorten erheblich von den standardisierten Testumgebungen, unter denen PV-Module gemäß den internationalen Normen IEC 61215 (Bauartprüfung) und IEC 61730 (Sicherheitsprüfung) geprüft und zertifiziert werden. Während diese Normen die allgemeine Widerstandsfähigkeit gegen Witterungseinflüsse wie UV-Strahlung, Feuchtigkeit und Temperaturwechsel testen, bleiben spezifische Belastungen durch chemisch-aggressive Atmosphären weitgehend unberücksichtigt. In landwirtschaftlichen Umgebungen können hohe Konzentrationen von Ammoniakgasen in Kombination mit Staubpartikeln auftreten, während in Kläranlagen insbesondere Schwefelwasserstoff, Ammoniak, hohe Luftfeuchtigkeit und andere korrosive Gase die Betriebsumgebung prägen.
Standard-PV-Module und -Systemkomponenten, die für den herkömmlichen Außeneinsatz konzipiert wurden, sind unter diesen Bedingungen oft nicht ausreichend beständig. Ohne gezielte Anpassung besteht das Risiko einer beschleunigten Materialdegradation, was sich negativ auf die Leistung, Lebensdauer und Betriebssicherheit der Anlagen auswirken kann. Zu den möglichen Folgen gehören unter anderem eine Verschlechterung der Verkapselungsmaterialien, Korrosion elektrischer Kontakte, mechanische Schwächung von Rahmen und Montagestrukturen sowie Leistungsverluste durch Verschmutzung oder Potenzial-induzierte Degradation (PID). Diese Effekte können kaskadenartig wirken und zum vorzeitigen Ausfall wesentlicher Komponenten führen – mit erheblichen Konsequenzen für die Rentabilität der Anlage.
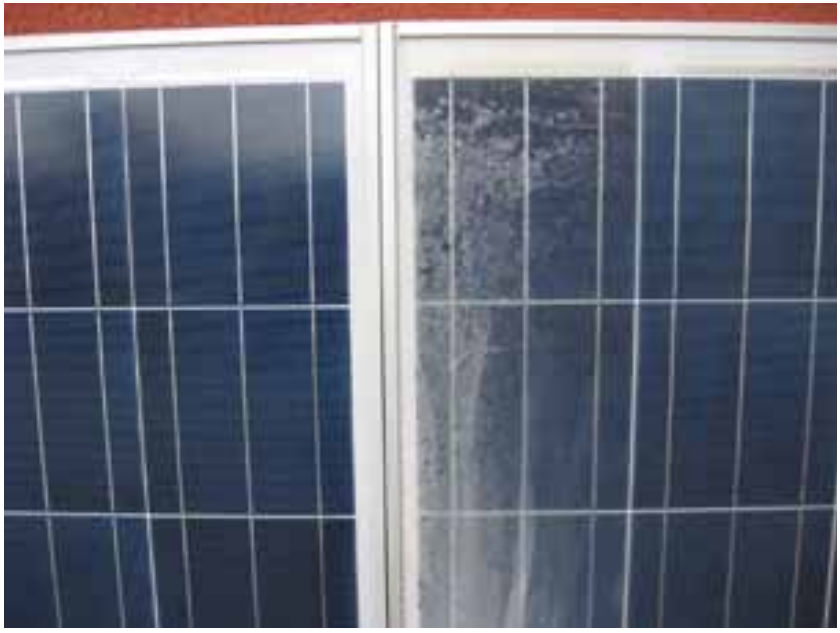
Abbildung 1: Vergleich PV-Module vor und nach DGL-Ammoniaktest
Ziel dieses Berichts ist es daher, die spezifischen Risiken und technischen Herausforderungen beim Einsatz von Standard-Photovoltaiksystemen in aggressiven Umgebungen – insbesondere in der Landwirtschaft und im Umfeld von Abwasserbehandlungsanlagen – systematisch zu analysieren. Der Fokus liegt auf den chemisch-physikalischen Belastungsfaktoren, den damit verbundenen Degradationsmechanismen und ihren Auswirkungen auf die Systemleistung und -lebensdauer. Zudem werden die Grenzen herkömmlicher Moduldesigns aufgezeigt und spezialisierte Zertifizierungen wie der DLG-FokusTest, die IEC 62716 für Ammoniakkorrosion sowie die IEC 61701 für Salznebelkorrosion als Bewertungsmaßstäbe herangezogen.
Ein fundiertes Verständnis dieser Problemfelder ist für alle involvierten Akteure – von Projektentwicklern über Investoren und Versicherer bis hin zu Anlagenbetreibern – von zentraler Bedeutung. Nur so lassen sich fundierte Entscheidungen über Technologieauswahl, Standortbewertung und langfristige Betriebskonzepte treffen. Die bewusste Berücksichtigung der Umweltbedingungen schützt nicht nur die Investition vor unerwarteten Ausfällen und Ertragseinbußen, sondern erhöht auch die Sicherheit und Nachhaltigkeit des Anlagenbetriebs. Werden hingegen die spezifischen Belastungen dieser Sonderumgebungen ignoriert, kann dies erhebliche technische und wirtschaftliche Nachteile nach sich ziehen.
2. Charakterisierung der aggressiven Betriebsumgebungen
Photovoltaikanlagen werden zunehmend in Umgebungen installiert, die weit über die Bedingungen standardisierter Prüfverfahren hinausgehen. Besonders herausfordernd sind landwirtschaftliche Betriebe sowie die Umgebung von Kläranlagen, da sie durch spezifische chemische und physikalische Belastungen geprägt sind. Diese Einflüsse wirken sich direkt auf die Haltbarkeit und Leistung von PV-Komponenten aus und erfordern daher eine differenzierte Betrachtung.
In landwirtschaftlichen Betrieben stellt insbesondere Ammoniak (NH₃) eine kritische Belastungsgröße dar. Es entsteht hauptsächlich durch den mikrobiellen Abbau von Harnstoff in tierischen Exkrementen und wird insbesondere in Ställen sowie bei der Lagerung und Ausbringung von Wirtschaftsdüngern freigesetzt. In geschlossenen Tierhaltungsanlagen, etwa Schweineställen, können Ammoniakkonzentrationen in der Luft Werte von 40 bis 50 ppm erreichen. In unmittelbarer Nähe von Abluftöffnungen – häufige Installationsorte für PV-Module – sind sogar noch höhere Werte möglich. Ammoniak ist nicht nur ein Luftschadstoff, der zur Versauerung von Böden und Gewässern beiträgt, sondern reagiert auch mit Luftfeuchtigkeit und Oberflächenmaterialien, wodurch potenziell korrosive Verbindungen entstehen.
Zusätzlich stellt Staub in der Landwirtschaft ein erhebliches Problem dar. Dieser besteht aus einem Gemisch aus organischen und mineralischen Partikeln – etwa aufgewirbelter Erde, Futterresten, Tierhaaren, Hautschuppen, Einstreumaterialien und getrocknetem Kot. Die Partikelgrößen reichen von grobem Schmutz bis hin zu feinem Aerosolstaub, der sich insbesondere in der Nähe von Lüftungsauslässen mit ammoniakhaltiger Feuchtigkeit verbinden kann. Diese Kombination bildet einen klebrigen, schwer entfernbaren Belag auf Oberflächen, der die Reinigungsfähigkeit reduziert und die Kontaktzeit korrosiver Substanzen mit den Modulkomponenten verlängert. Dadurch wird die natürliche Selbstreinigung der PV-Module durch Regen ineffektiv, was langfristig zu stärkerem Verschleiß führen kann.
Die Gleichzeitigkeit von Ammoniak, Staub und Feuchtigkeit führt zu einem besonders aggressiven Umfeld für PV-Module. Feuchte Staubschichten binden Ammoniak und verlängern die Exposition gegenüber chemisch aktiven Stoffen, was die Degradation von Materialien wie Dichtungen, Folien oder Metallkontakten beschleunigt. Durch diese synergetische Belastung steigt das Risiko mechanischer und elektrischer Schäden erheblich.
Auch in Kläranlagen ist Ammoniak präsent, doch tritt hier zusätzlich ein weiterer, besonders aggressiver Schadstoff auf: Schwefelwasserstoff (H₂S). Dieses Gas entsteht unter anaeroben Bedingungen durch die Aktivität sulfatreduzierender Bakterien, insbesondere in Sammelkanälen, Vorklärbecken, Faulbehältern und Schlammbehandlungsanlagen. H₂S ist giftig, geruchsintensiv (Geruch nach faulen Eiern) und bei hoher Konzentration gefährlich. Da es schwerer als Luft ist, sammelt es sich in tiefergelegenen Bereichen und schlecht belüfteten Zonen an – genau dort, wo PV-Komponenten installiert sein können.
Von besonderer Relevanz ist der Prozess der biogenen Schwefelsäurekorrosion, der in Kläranlagenumgebungen auftreten kann. In Gegenwart von Feuchtigkeit und sogar geringer Sauerstoffkonzentration oxidieren spezielle Bakterien wie Thiobacillus den Schwefelwasserstoff zu Schwefelsäure (H₂SO₄), eine äußerst aggressive Verbindung. Dieser Mechanismus ist aus der Betonkorrosion bekannt, kann aber auch auf Metallstrukturen wie PV-Rahmen, Montagesysteme oder elektrische Kontakte wirken. Da Kläranlagen durchgehend hohe Luftfeuchtigkeit aufweisen – verursacht durch offene Wasserflächen, Sprühnebel und Verdunstung – wird dieser Prozess zusätzlich verstärkt. Kondenswasserbildung auf Moduloberflächen bei Temperaturschwankungen ist keine Seltenheit, was die Materialbeanspruchung weiter erhöht.
Zudem sind Kläranlagen atmosphärisch komplexe Umgebungen, in denen neben H₂S und NH₃ auch flüchtige organische Verbindungen (VOCs), saure oder alkalische Dämpfe sowie industrielle Rückstände auftreten können – abhängig von der Herkunft des eingeleiteten Abwassers. Diese Mischung kann die Korrosivität der Luft weiter verstärken und stellt eine zusätzliche Herausforderung für PV-Komponenten dar, deren Materialauswahl und Dichtungskonzepte nicht auf solche Einflüsse ausgelegt sind.
Insgesamt lässt sich festhalten, dass sowohl landwirtschaftliche als auch abwassertechnische Umgebungen eine signifikante und komplexe Belastung für PV-Anlagen darstellen. Die hier vorherrschenden atmosphärischen Bedingungen – hohe Konzentrationen aggressiver Gase, Feuchtigkeit, Schwebstoffe und temperaturbedingte Kondensation – wirken nicht nur einzeln, sondern oft in Wechselwirkung miteinander. Dies führt zu multiplen Degradationsmechanismen, deren kombinierte Wirkung deutlich stärker ist als die Summe der Einzeleffekte. Um eine langfristig stabile, leistungsfähige und wirtschaftlich tragfähige Nutzung von PV-Anlagen in solchen Umgebungen zu gewährleisten, ist daher eine gezielte Auswahl geeigneter Materialien, Komponenten und Zertifizierungen zwingend erforderlich.
3. Anfälligkeit von Standard-PV-Modulkomponenten
Standard-Photovoltaikmodule sind für typische Außenbedingungen konzipiert und durchlaufen Prüfverfahren gemäß den Normen IEC 61215 und IEC 61730, die sie unter simulierten Witterungseinflüssen testen. In den besonders aggressiven Umgebungen der Landwirtschaft und Kläranlagen sind die Module jedoch chemischen und physikalischen Belastungen ausgesetzt, die über die vorgesehenen Standardszenarien hinausgehen. Dies betrifft insbesondere den Einfluss von Ammoniak, Schwefelwasserstoff, hoher Luftfeuchtigkeit sowie Staub und Verschmutzung, welche sich erheblich auf die einzelnen Modulkomponenten auswirken können.
Ein zentrales Problem stellt die durch Ammoniak verursachte Materialdegradation dar. Ammoniak, vor allem in feuchter Umgebung, kann tief in die polymeren Schutzschichten eines PV-Moduls eindringen. Besonders betroffen sind dabei die Verkapselungsmaterialien wie Ethylenvinylacetat (EVA) sowie die Rückseitenfolien, die häufig aus Polyethylenterephthalat (PET), Polyvinylfluorid (PVF) oder Polyamid (PA) bestehen. Durch chemische Reaktionen wie die Hydrolyse von Esterbindungen kann es zur Versprödung, Verfärbung und letztlich Delamination kommen – dem Ablösen der einzelnen Schichten im Laminataufbau. Diese Delamination gefährdet den Schutz der Solarzellen vor Umwelteinflüssen und kann in der Folge die elektrische Isolation und Funktionsfähigkeit des Moduls massiv beeinträchtigen.
Dringt Ammoniak weiter in das Innere des Moduls vor, kann es dort metallische Strukturen wie Zellfinger, Busbars oder Zellverbinder korrodieren. In Gegenwart von Feuchtigkeit bildet Ammoniak eine alkalische Lösung, die unter anderem Silber und Kupfer angreift – Materialien, die essenziell für die Stromführung innerhalb des Moduls sind. Die entstehenden Schäden können den Serienwiderstand erhöhen, was sich unmittelbar in Leistungsverlusten äußert. Im Extremfall kommt es zu Kontaktunterbrechungen und damit zum Ausfall einzelner Zellen oder ganzer Modulbereiche.
Auch die Anschlussdosen und Steckverbinder von Standardmodulen sind anfällig. Gummidichtungen können durch die chemische Belastung verspröden, während Kunststoffgehäuse durch Langzeiteinwirkung ihre mechanische Integrität verlieren. Besonders kritisch ist die Korrosion elektrischer Kontakte in diesen Komponenten: Sie kann zu erhöhten Übergangswiderständen, lokalen Überhitzungen (Hot Spots) und letztlich zur Brandgefahr führen. Obwohl es speziell entwickelte, ammoniakbeständige Steckverbindersysteme und Dichtmaterialien gibt, sind diese nicht in Standardmodulen enthalten, es sei denn, sie wurden gezielt für solche Umgebungen spezifiziert.
Ein weiteres häufig unterschätztes Problem ist die Korrosion von Modulrahmen. Zwar weisen Aluminiumrahmen durch ihre natürliche Oxidschicht oder eine anodische Beschichtung eine gewisse Grundbeständigkeit auf, doch kann diese Schicht durch mechanische Einwirkungen (z. B. Montagefehler, Reinigungswerkzeuge) beschädigt werden. In Verbindung mit ammoniakalischer Feuchtigkeit oder sauren Gasen wie H₂S kann es dann zu Lochfraß oder flächiger Korrosion kommen. Dies beeinträchtigt nicht nur die strukturelle Stabilität, sondern kann auch die elektrische Erdung gefährden – ein wesentliches Sicherheitskriterium im Betrieb.
Noch gravierender ist die Situation in Kläranlagenumgebungen. Dort führt die Anwesenheit von Schwefelwasserstoff in Kombination mit Feuchtigkeit zu besonders aggressiven Bedingungen. H₂S wird durch Bakterien in Schwefelsäure umgewandelt, die Metalle massiv angreift. Selbst rostfreier Stahl kann unter solchen Bedingungen über längere Zeiträume geschädigt werden, insbesondere wenn sich aufgrund von Materialkombinationen galvanische Korrosion einstellt. Aluminiumlegierungen und verzinkter Stahl – häufige Materialien in Standard-Montagesystemen – sind hier besonders anfällig und zeigen frühzeitige Korrosionserscheinungen, die zu einem Versagen der mechanischen Halterungen führen können.
Auch Wechselrichter, obwohl in geschlossenen Gehäusen verbaut, können bei unzureichendem Schutz vor kontaminierter Luft oder mangelhafter Dichtigkeit durch H₂S und feuchte Umgebungsluft geschädigt werden. Schwefelverbindungen können auf Platinen und Kontakte wirken, was zu Fehlfunktionen oder vollständigem Versagen führen kann. Der Schutzgrad (IP-Klassifizierung) der eingesetzten Komponenten ist daher von entscheidender Bedeutung, ebenso wie ihre Platzierung im Anlagenlayout.
Neben chemischen Angriffen stellen auch Staub und Feuchtigkeit eine signifikante Belastung dar. Staubablagerungen auf den Moduloberflächen vermindern den Lichteinfall und reduzieren so direkt den Energieertrag. Besonders problematisch sind klebrige Mischbeläge aus Staub und ammoniakhaltiger Feuchtigkeit, die sich nur schwer durch Regen entfernen lassen. Ohne regelmäßige Reinigung können Ertragsverluste von bis zu 30 % auftreten. Darüber hinaus wirkt abrasiver Staub langfristig auch mechanisch auf die Moduloberfläche: Er kann die Antireflexionsschicht beschädigen und Mikrokratzer erzeugen, die die Neigung zur Schmutzanhaftung und damit zur weiteren Degradation erhöhen.
Feuchtigkeit wiederum kann durch alternde Dichtungen oder Mikrorisse in das Modulinnere eindringen – insbesondere, wenn diese durch thermische Belastung, UV-Einwirkung oder chemische Alterung geschwächt sind. Dies führt nicht nur zu Korrosion der Zellverbindungen, sondern erhöht auch die Anfälligkeit für Potenzial-induzierte Degradation (PID). Dieser Effekt tritt bei hoher Systemspannung auf, wenn durch Feuchtigkeit und kontaminierte Oberflächen Leckströme fließen, die zu erheblichen Leistungsverlusten führen können. In Kombination mit aggressiven Schadstoffen aus der Umgebung (z. B. Salze oder Ammoniakverbindungen) wird PID noch weiter begünstigt.
Ein zusätzlicher Aspekt betrifft die Reinigung: In stark belasteten Umgebungen wie der Landwirtschaft sind häufige Reinigungsmaßnahmen notwendig, um Verschmutzungsverluste zu minimieren. Wird hierbei jedoch mit ungeeigneten Mitteln oder Werkzeugen gearbeitet – etwa mit harten Bürsten, Hochdruckreinigern oder aggressiven Chemikalien – können Modulmaterialien zusätzlich geschädigt werden. Selbst hartes Leitungswasser kann durch Kalkablagerungen den Ertrag mindern. Dadurch wird die eigentlich notwendige Reinigungsmaßnahme selbst zu einem Risikofaktor für die Modulintegrität, wenn sie nicht fachgerecht durchgeführt wird.
Zusammenfassend lässt sich festhalten, dass Standard-PV-Komponenten unter den beschriebenen extremen Umgebungsbedingungen erheblichen Risiken ausgesetzt sind. Die Kombination aus chemischer Korrosion, Materialalterung, mechanischem Abrieb und Feuchtigkeitseintritt führt zu einer Vielzahl von Degradationsprozessen, die sich gegenseitig verstärken können. Ohne gezielte Anpassung der eingesetzten Materialien und Komponenten ist ein zuverlässiger und langfristig wirtschaftlicher Betrieb in diesen Umgebungen kaum möglich.
5. Spezialisierte Module und relevante Zertifizierungen
Der Einsatz von Photovoltaikanlagen in rauen und chemisch belasteten Umgebungen wie Tierställen oder Kläranlagen erfordert Komponenten, die weit über den Standardanforderungen der PV-Industrie hinausgehen. Während Standardmodule primär für typische Außenbedingungen entwickelt und gemäß den Normen IEC 61215 und IEC 61730 getestet werden, sind sie gegenüber besonderen Belastungen – etwa durch Ammoniak, Schwefelwasserstoff oder hohe Luftfeuchtigkeit – oft nur unzureichend geschützt. Um die Betriebssicherheit, Leistungsstabilität und Lebensdauer von PV-Anlagen auch unter diesen erschwerten Bedingungen sicherzustellen, wurden spezialisierte Moduldesigns und ergänzende Zertifizierungen entwickelt.
Ein wesentlicher Schlüssel zur Eignung solcher Module liegt in der Auswahl widerstandsfähigerer Materialien und robusterer Bauweisen. Im Bereich der Ammoniakbeständigkeit – ein zentrales Thema in landwirtschaftlichen Umgebungen – werden zunehmend hochresistente Kunststoffe wie modifizierte Polyphenylenether (z. B. XYRON™) eingesetzt. Diese Materialien zeichnen sich durch eine hohe chemische Stabilität aus und eignen sich besonders für Rückseitenfolien oder Anschlussdosen, die in Kontakt mit ammoniakhaltiger Luft stehen können. Auch die Auswahl spezieller Verkapselungsmaterialien sowie langlebiger Dichtsysteme trägt maßgeblich dazu bei, das Eindringen von Gasen und Feuchtigkeit in das Modulinnere zu verhindern.
Ein weiteres konstruktives Element sind nichtmetallische Modulrahmen aus Polyurethan-Kompositen oder glasfaserverstärktem Kunststoff (GFK), die gegenüber korrosiven Substanzen eine weitaus höhere Resistenz zeigen als klassische Aluminiumrahmen. Zudem bieten sogenannte Glas-Glas-Module – bei denen die Solarzellen vollständig von Glas eingeschlossen sind – durch ihre dichte Struktur einen besseren Schutz gegenüber Feuchtigkeit und gasförmigen Schadstoffen als Module mit polymerer Rückseitenfolie.
In Umgebungen mit hoher Korrosionsbelastung, wie sie typischerweise in Kläranlagen auftreten, sind korrosionsbeständige Montagesysteme und Modulrahmen entscheidend. Hier kommen etwa besonders legierte Edelstähle, dick beschichtete Aluminiumlegierungen oder sogar nichtmetallische Tragstrukturen zum Einsatz. Die verwendeten Steckverbinder und Anschlussdosen müssen ebenfalls speziell ausgewählt werden, da feuchte und saure Atmosphären auch diese Komponenten stark angreifen können. Eine besonders hohe Qualität der Modulversiegelung sowie eine sorgfältige Verarbeitung sind für den langfristigen Schutz gegen eindringende Schadstoffe unerlässlich.
Zur objektiven Bewertung der Eignung von PV-Modulen für solche anspruchsvollen Umgebungen wurden spezielle Prüfstandards entwickelt, die ergänzend zu den Basistests der IEC 61215/61730 durchgeführt werden. Einer der bedeutendsten ist der DLG FokusTest Ammoniakbeständigkeit, der von der Deutschen Landwirtschafts-Gesellschaft speziell für den Einsatz in der Tierhaltung konzipiert wurde. In einer Klimakammer werden die Prüflinge über einen langen Zeitraum (typisch 1500 Stunden) hohen Ammoniakkonzentrationen (z. B. 750 ppm), Temperaturen bis 70 °C und relativer Luftfeuchte von etwa 70 % ausgesetzt. Bewertet werden neben dem Leistungsabfall (zulässig sind maximal 5 %) auch die elektrische Isolation sowie sichtbare Veränderungen wie Risse oder Vergilbung. Auch Steckverbinder können in diesen Test einbezogen werden, um ihren Kontaktwiderstand unter Belastung zu bewerten.
International anerkannt ist zudem die IEC 62716, die sich ebenfalls mit der Ammoniakbeständigkeit befasst, jedoch unter standardisierten Bedingungen. Die Prüfkammerbedingungen beinhalten meist eine Ammoniakkonzentration von rund 6667 ppm über mehrere Zyklen à 24 Stunden. Auch hier gilt: Sichtbare Mängel, Isolationsfehler oder eine Leistungsdegradation über 5 % führen zum Nichtbestehen.
Für Standorte mit hoher allgemeiner Korrosionsbelastung, insbesondere in maritimen oder abwassertechnischen Umgebungen, ist die IEC 61701 zur Bewertung der Salznebelkorrosionsbeständigkeit von zentraler Bedeutung. In dieser Prüfung werden die Module in einer Kammer zyklisch mit einer Salzlösung (zumeist Natriumchlorid) beaufschlagt und unter wechselnden Feuchtigkeitsbedingungen getestet. Die Norm unterscheidet zwischen mehreren Schärfegraden (Severity Levels), wobei Stufe 6 die härteste Form darstellt und eine Prüfzeit von 56 Tagen (8 Zyklen à 7 Tage) umfasst. Module, die diese Prüfung erfolgreich bestehen, demonstrieren eine besonders gute Materialwahl, hochwertige Versiegelung und allgemein robuste Verarbeitung – Eigenschaften, die auch in feuchten, schwefelwasserstoffbelasteten Kläranlagen einen Schutz vor Korrosion bieten.
Obwohl es derzeit keine spezifische IEC-Norm zur Prüfung der H₂S-Beständigkeit von PV-Modulen gibt, kann ein erfolgreich bestandener Salznebeltest auf hohem Schärfegrad dennoch als Indikator für eine generelle Korrosionsbeständigkeit gewertet werden. Die in beiden Fällen wirksamen elektrochemischen Korrosionsprozesse ähneln sich in ihrer Wirkung auf metallische Komponenten und Dichtmaterialien. Daher kann die IEC 61701 (insbesondere auf Level 6) als Proxy-Indikator für die Tauglichkeit eines Moduls in Kläranlagenumgebungen herangezogen werden.
Die folgende Gegenüberstellung zeigt die relevanten Zertifizierungen im Überblick: Während IEC 61215/61730 die Basiszertifizierung für PV-Module darstellen und lediglich die allgemeine Eignung für Außenanwendungen sicherstellen, adressiert der DLG FokusTest explizit die extremen Bedingungen in der Tierhaltung. Die IEC 62716 stellt einen international harmonisierten Standard für Ammoniakumgebungen dar und ist insbesondere für Hersteller mit globaler Ausrichtung relevant. Die IEC 61701 wiederum zielt auf salzhaltige bzw. allgemein korrosive Umgebungen ab und gewinnt zunehmend an Bedeutung für Anwendungen im Küstenbereich sowie – indirekt – für den Einsatz in Kläranlagen.
Ein PV-Modul, das eine oder mehrere dieser erweiterten Prüfungen erfolgreich absolviert hat, weist eine nachgewiesene höhere Resistenz gegenüber spezifischen Umweltbelastungen auf. Solche Produkte stellen daher die bevorzugte Wahl für Installationen in anspruchsvollen Umgebungen dar. Gleichzeitig liefern diese Zertifizierungen Projektentwicklern, Investoren und Versicherern eine verlässliche Entscheidungsgrundlage bei der Auswahl geeigneter Technologien und ermöglichen eine Absicherung gegen Garantieausschlüsse, die im Zusammenhang mit chemischer Belastung häufig vertraglich ausgeschlossen sind.
6. Synthese potenzieller Probleme: Ein konsolidierter Blick auf die Risiken
Die Analyse der Umgebungsbedingungen sowie der materialspezifischen Schwachstellen von Standard-Photovoltaikmodulen zeigt deutlich, dass der Einsatz solcher Systeme in landwirtschaftlichen und abwassertechnischen Umgebungen mit erheblichen Risiken verbunden ist. Diese Risiken sind nicht isoliert zu betrachten, sondern ergeben sich aus einer Vielzahl ineinandergreifender Degradationsprozesse, die sich gegenseitig verstärken können – ein komplexes Zusammenspiel chemischer, physikalischer und elektrischer Einflüsse.
Ein zentrales Problem besteht in der kaskadierenden Materialdegradation, bei der zunächst äußere Schutzstrukturen wie die Rückseitenfolie, Verkapselung oder Modulrahmen durch chemisch-aggressive Gase wie Ammoniak oder Schwefelwasserstoff angegriffen werden. In feuchter Umgebung beschleunigt sich dieser Prozess, da die chemischen Substanzen in Lösung gehen und so effektiver mit den Materialien reagieren können. Die dadurch geschwächte Barrierefunktion der Module erlaubt es Schadstoffen, tiefer in das Laminat einzudringen. Sobald die inneren Schichten betroffen sind – insbesondere Zellverbindungen, Lötstellen und metallische Kontakte –, entsteht ein sich selbst verstärkender Degradationsprozess. Korrosion im Zellinneren und Delamination der Verkapselung begünstigen den Eintritt weiterer Feuchtigkeit und Schadstoffe, was die elektrische Integrität und mechanische Stabilität des Moduls nachhaltig beeinträchtigt.
Parallel dazu ergibt sich eine deutliche Verschlechterung der Leistungsfähigkeit der Anlage. Bereits kurzfristig führen klebrige Staub-Ammoniak-Beläge oder biologische Verunreinigungen zu erheblichen Ertragseinbußen, da sie die Lichtdurchlässigkeit der Moduloberfläche mindern. Zwar sind diese Verluste durch Reinigung grundsätzlich reversibel, doch in vielen Fällen ist die Ablagerung so hartnäckig, dass einfache Reinigungsmechanismen – wie Regen – nicht ausreichen. Langfristig wird der Leistungsverlust jedoch zunehmend durch irreversible Prozesse wie Korrosion, Materialermüdung oder Potenzial-induzierte Degradation (PID) bestimmt. PID ist insbesondere in feuchten, hochspannungsführenden Systemen problematisch und kann durch kontaminierte Oberflächen zusätzlich verstärkt werden. Diese kombinierte Belastung führt dazu, dass sich die tatsächliche Degradationsrate deutlich über den für Standardumgebungen typischen Werten von 0,5 bis 0,8 Prozent pro Jahr bewegt.
Ein weiteres zentrales Risiko ist die Verkürzung der Lebensdauer und abnehmende Systemzuverlässigkeit. Module, deren Materialien durch die genannten Umwelteinflüsse vorzeitig altern oder versagen, erreichen nicht die projektierte Lebensdauer von 25 bis 30 Jahren. Oftmals treten nicht nur kontinuierliche Leistungsminderungen auf, sondern plötzliche Ausfälle durch Hot Spots, gebrochene Kontakte oder beschädigte Steckverbindungen. Hinzu kommt die mögliche Schädigung tragender Montagestrukturen, insbesondere in Kläranlagen, wo korrosive Atmosphären die Integrität von verzinktem Stahl oder Aluminium gefährden können. Solche strukturellen Schäden können dazu führen, dass ganze Modulreihen instabil werden, sich lösen oder sogar Sicherheitsfunktionen wie die Erdung nicht mehr gewährleistet sind.
Damit eng verknüpft sind erhebliche Sicherheitsrisiken. Korrodierte Erdungspfade, durchfeuchtete Anschlussdosen oder porös gewordene Isoliermaterialien erhöhen die Wahrscheinlichkeit elektrischer Defekte, etwa durch Lichtbögen oder Kurzschlüsse. In Extremfällen besteht Brandgefahr – ein Risiko, das nicht nur die Anlage selbst, sondern auch angrenzende Infrastrukturen oder Personen gefährden kann. Besonders in automatisierten Betriebsumgebungen, etwa in Klärwerken oder modernen Tierhaltungsbetrieben, in denen elektrische Sicherheit höchste Priorität hat, kann dies gravierende Folgen haben – bis hin zum Betriebsstopp.
All diese technischen Herausforderungen führen zu direkten ökonomischen Konsequenzen. Eine schnellere Degradation, höhere Ausfallraten und häufiger Wartungsbedarf bedeuten steigende Betriebskosten. Hinzu kommen mögliche Ertragsausfälle durch Leistungseinbußen oder zeitweilige Abschaltungen der Anlage. Nicht selten sind diese Kosten deutlich höher als ursprünglich kalkuliert, da Standardgarantien der Modulhersteller in der Regel keine Schadensfälle abdecken, die auf chemisch-aggressive oder nicht standardisierte Umgebungen zurückzuführen sind. Ohne geeignete, speziell zertifizierte Komponenten besteht daher nicht nur ein erhöhtes technisches, sondern auch ein finanzielles Risiko für Betreiber und Investoren.
Dass diese Problematik nicht rein theoretischer Natur ist, zeigt sich auch daran, dass bereits spezialisierte Module und Testverfahren für solche Einsatzszenarien existieren. Die Entwicklung von Prüfstandards wie dem DLG-FokusTest oder der IEC 62716 und IEC 61701 unterstreicht, dass die Industrie auf reale Problemstellungen reagiert hat. Gleichzeitig mangelt es derzeit noch an umfassenden Langzeitstudien zu bestehenden Anlagen unter den hier beschriebenen Bedingungen. Erste Erfahrungen mit Agri-PV-Installationen oder schwimmenden PV-Anlagen auf Klärbecken deuten jedoch auf ein wachsendes Problembewusstsein hin – auch wenn viele Projekte noch im Pilotstadium sind.
7. Empfehlungen für den Einsatz von PV-Anlagen in anspruchsvollen Umgebungen
Auf Grundlage der vorangegangenen Analyse ergibt sich ein klarer Handlungsbedarf für die Planung, Auslegung und den Betrieb von Photovoltaikanlagen in chemisch und klimatisch belasteten Umgebungen wie landwirtschaftlichen Betrieben und Kläranlagen. Die Risiken für Materialversagen, Leistungsminderung und Sicherheitsprobleme sind in solchen Einsatzszenarien deutlich erhöht. Um diesen Herausforderungen wirkungsvoll zu begegnen, sind gezielte Maßnahmen auf mehreren Ebenen erforderlich – von der Standortbewertung über die Auswahl geeigneter Komponenten bis hin zur langfristigen Betriebs- und Wartungsstrategie.
Ein erster und grundlegender Schritt besteht in einer sorgfältigen Umweltbewertung vor Ort. Dabei sollten die spezifischen Belastungen des geplanten Standorts möglichst detailliert erfasst werden. Dies umfasst insbesondere die Konzentrationen und Eintragsquellen von Ammoniak und Schwefelwasserstoff, die relative Luftfeuchtigkeit, das Verschmutzungsniveau durch Staub und Aerosole sowie die Nähe zu Emissionsquellen wie Stalllüftungen oder offenen Klärbecken. Je nach Ergebnis dieser Analyse können die Anforderungen an die eingesetzten Komponenten präzise definiert werden.
Für Standorte mit signifikanter Ammoniakbelastung – wie sie insbesondere in der Tierhaltung typisch sind – sollten ausschließlich PV-Module mit entsprechender Ammoniakzertifizierung eingesetzt werden. Dabei gilt: Die IEC 62716 stellt einen international anerkannten Mindeststandard dar, während der DLG FokusTest zusätzliche Sicherheit für Langzeitbeständigkeit in realistischen Stallszenarien bietet. Bei Einsatzorten in oder nahe Kläranlagen empfiehlt sich der Einsatz von Modulen mit bestandener Salznebelprüfung nach IEC 61701, vorzugsweise auf hohem Schärfegrad (z. B. Stufe 6), um die Eignung für feuchte und korrosive Atmosphären sicherzustellen. Da Ammoniak zusätzlich eine Rolle spielt, sollte ergänzend die IEC 62716 vorliegen.
Die sorgfältige Auswahl sämtlicher Systemkomponenten ist ebenso entscheidend. Neben den Modulen selbst betrifft dies die Montagestrukturen, Wechselrichter, Steckverbinder und elektrischen Schutzkomponenten. Die Montagesysteme müssen hinsichtlich ihrer Korrosionsbeständigkeit ausgelegt sein – je nach Einsatzort empfiehlt sich etwa der Einsatz von V4A-Edelstahl, spezialbeschichteten Aluminiumprofilen oder GFK-basierten Konstruktionen. Bei der Kombination unterschiedlicher Materialien sollte auf das elektrochemische Korrosionspotenzial geachtet werden, um galvanische Korrosion zu vermeiden. Anschlussdosen, Kabel und Steckverbinder müssen ebenfalls chemikalienbeständig und für den Einsatz in feuchten Umgebungen geeignet sein, idealerweise mit geprüfter Schutzart IP65 oder höher.
Auch das Systemdesign selbst sollte an die Umgebungsbedingungen angepasst werden. So kann etwa eine gezielte Erdungsstrategie helfen, das Risiko für PID zu reduzieren. Eine gute Hinterlüftung der Module beugt Feuchtigkeitsansammlungen vor und senkt die Betriebstemperaturen – beides wirkt sich positiv auf die Lebensdauer der Komponenten aus. Die Positionierung der PV-Module sollte möglichst entfernt von direkten Emissionsquellen erfolgen; wo dies nicht möglich ist, können bauliche Maßnahmen wie Abluftumlenkung oder zusätzliche Schutzabdeckungen sinnvoll sein.
Ein weiterer zentraler Aspekt ist die Entwicklung und Umsetzung einer maßgeschneiderten Betriebs- und Wartungsstrategie. In stark belasteten Umgebungen reichen Standard-O&M-Protokolle nicht aus. Die Reinigungsintervalle müssen dem Verschmutzungsgrad angepasst werden und dürfen nur mit geeigneten Mitteln und Methoden durchgeführt werden – dazu gehören demineralisiertes Wasser, weiche Bürsten und der Verzicht auf aggressive Reinigungschemikalien oder Hochdruckgeräte. Auch die Wasserhärte muss beachtet werden, um Kalkablagerungen zu vermeiden. Regelmäßige Inspektionen sollten insbesondere den Zustand von Rahmen, Dichtungen, Anschlussdosen, Steckverbindern und Tragsystemen berücksichtigen. Frühzeitige Anzeichen von Korrosion, Delamination oder Verfärbungen können auf größere Probleme hindeuten und sollten zeitnah behandelt werden.
Die kontinuierliche Leistungsüberwachung spielt eine ebenso wichtige Rolle. Moderne Monitoring-Systeme ermöglichen es, auch kleinste Leistungseinbrüche oder Auffälligkeiten im Stringverhalten frühzeitig zu erkennen. So können fehlerhafte Module oder PID-Probleme identifiziert werden, bevor sie sich negativ auf die gesamte Anlage auswirken. Ein datenbasiertes Monitoring bildet die Grundlage für präventive Wartung und reduziert langfristig die Ausfallzeiten.
Ebenfalls zu empfehlen ist eine frühzeitige Abstimmung mit Herstellern, Versicherern und Finanzierern. Die besondere Beanspruchung durch chemisch-aggressive Umgebungen muss offen kommuniziert und in den Garantie- und Versicherungsbedingungen explizit berücksichtigt werden. Nur wenn die eingesetzten Produkte für diese Bedingungen zertifiziert sind, besteht eine realistische Chance auf erweiterte Garantien oder den Einschluss solcher Risiken in Policen. Auch bei Ausschreibungen und Förderanträgen sollte der erhöhte technische Anspruch dokumentiert werden, um Fehlinvestitionen zu vermeiden.
Letztlich sollte der Fokus nicht nur auf der Reduktion kurzfristiger Investitionskosten liegen, sondern auf dem langfristigen Werterhalt der Anlage. Zwar erscheinen spezialisierte Komponenten auf den ersten Blick teurer, doch amortisiert sich der Mehraufwand durch reduzierte Ausfallwahrscheinlichkeit, geringeren Wartungsbedarf und stabilere Erträge über den gesamten Lebenszyklus der Anlage. Eine technisch fundierte Komponentenauswahl, die auf belastbare Zertifizierungen basiert, ist daher nicht nur eine Frage der Betriebssicherheit, sondern vor allem auch ein wirtschaftlich rationaler Schritt – insbesondere in Umgebungen, die durch ihre physikalisch-chemischen Eigenschaften ein besonders hohes Risiko darstellen.